Is a top running or underhung bridge crane appropriate for your facility?
Learn more about how to make this determination, the pros and cons of each configuration, and factors to keep in mind as you evaluate what’s best for your business.
When selecting a bridge crane, there are several important design criteria that you will need to decide on, all of which could have significant implications for your crane’s day-to-day operation. One of these criteria is whether to use a top-running or underhung bridge crane.
In this article, we’ll discuss the difference between a top running bridge crane and an underhung bridge crane, evaluating some of the distinct advantages and disadvantages of each.
General Crane Terminology and Layout
To understand the difference between a top running crane and underhung crane, it’s first important to understand the basic components that make up a bridge crane system and, specifically, the components that allow the crane to move throughout the facility.
Runway Beams
These are structural members (I-beams) that run parallel to each other on the outsides of the facility space and are sized as needed to support the rated load of the crane. The runway beams don’t move during bridge crane operation – they are the supporting structure that hold up all the moving components. Mounted to the top of the runway beams are the runway rails, which are how the bridge crane is able to slide back and forth along the runway beam.
Bridge Girder
The bridge girder is the structural component that runs between the two runway beams, extending over the facility space that the crane is supporting. The bridge girder connects to the runway beam with what is called an “end truck”, which is the component that allows the entire assembly to slide over the runway rail that’s mounted to the runway beam. Depending on the size of the crane, a bridge crane can either have one or two bridge girders mounted between the runway beams, which is what distinguishes a “single-girder” bridge crane from a “double-girder” bridge crane.
Crane Trolley
The crane trolley moves back and forth along the bridge girder (or “girders” if the system is double girder) to facilitate movement in the opposite direction of the runway beams. So, for instance, if the runway beam allows movement in the north-south direction across the facility space, the bridge girders allow the crane trolley to move in the east-west direction. The crane hoist, itself, is mounted to the crane trolley, supporting the wire rope and hook which are what actually move up and down to lift the load.
The difference between top running vs. underhung
As you can see from the previous section, a bridge crane is comprised of multiple “layered” members that facilitate movement in different directions. There is a motor attached to the bridge girders that allow them to slide along the runway beam, and there is a motor attached to the trolley/hoist which allows it to slide along the bridge girders.
What distinguishes a “top running” bridge crane from an “underhung” bridge crane is how the trolley is mounted to the bridge girder system.
In the case of a top running bridge crane, the trolley and hoist are mounted to the top of the bridge girder(s), moving along bridge rails in a similar fashion to how the bridge girders slide along the runway beams. On an underhung bridge crane, however, the trolley and hoist are mounted to the bottom of the bridge girder and slide back and forth along the bottom flange of the girder.
Based on these configurations, it probably makes sense intuitively that a top-running bridge crane is better-designed to lift larger loads, while underhung cranes provide more flexibility for moving smaller loads throughout the space. In the following sections, we’ll break down some of the pros and cons of each system.
Top running bridge cranes
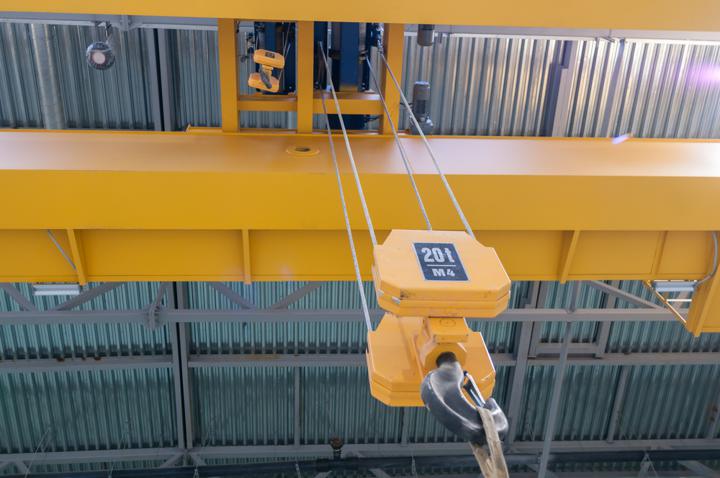
One of the main benefits of top running bridge cranes is that they can be designed to handle extreme loads. As such, they’re typically larger than underhung bridge cranes, so not only can they be rated for a higher capacity than an underhung bridge crane, but they can also accommodate wider spans between the runway beams due to the larger structural member sizes that make up the system.
Having the crane trolley mounted to the top of the bridge girders also provides benefits from a maintenance standpoint, facilitating easier access and serviceability. If an underhung bridge crane needs maintenance, it is likely that the crane trolley will have to be detached from the bridge girders for proper access. However, a top running bridge crane sits on top of the bridge girders, so a maintenance worker can perform the necessary activities in place as long as there are catwalks, or some other means of accessing the space.
A top running bridge crane can also provide significant benefits in areas with limited headspace. When you’re designing a bridge crane system, one of the most important factors to keep in mind is the top hook height you need, or the elevation of the hook at the highest position. In design, you typically need to think through the height of the tallest object that your bridge crane will need to hoist (considering the specific rigging configuration for the object), then determine the tallest object that this object will need to be designed to “leap-frog” over. In other words, you need to know how high you will be able to move the tallest object you are designing for above the operating floor.
In a facility with limited headroom, meaning that your bridge crane is located relatively low to the ground, an underhung bridge crane may not even be feasible for your application. You can typically achieve an extra 3 to 6 feet of hook height by switching from an underhung bridge crane to a top running bridge crane. On the flip side, having the trolley mounted to the top of the bridge girders can restrict movement throughout the space in some instances. As an example, if the roof of a facility is sloped and the bride girders are located near the ceiling, there may be restrictions on how close the bridge crane can get to the point where the ceiling meets the wall, limiting the amount of area that the crane can cover throughout the facility space.
A top running bridge crane can be either single girder or double girder. What distinguishes one from the other largely comes down to how much load capacity you need for the given application. Below are a few criteria to keep in mind as you evaluate the need for a single girder vs. double girder bridge crane.
Top Running Single Girder Crane
· Load Capacity: ¼-ton to 20 tons
· Typical Span: Under 65 feet
· Typical Service: Light to medium duty
· Faster hoist and trolley speed
· Less costly than double girder
· More flexibility of movement throughout the space
Top Running Double Girder Crane
· Load Capacity: 20-400 tons
· Typical Span: Over 65 feet
· Typical Service: Medium to heavy duty
· More costly
· Allows for the best lifting height and overhead floor space
· Less flexibility of movement throughout the space
Underhung Bridge Cranes
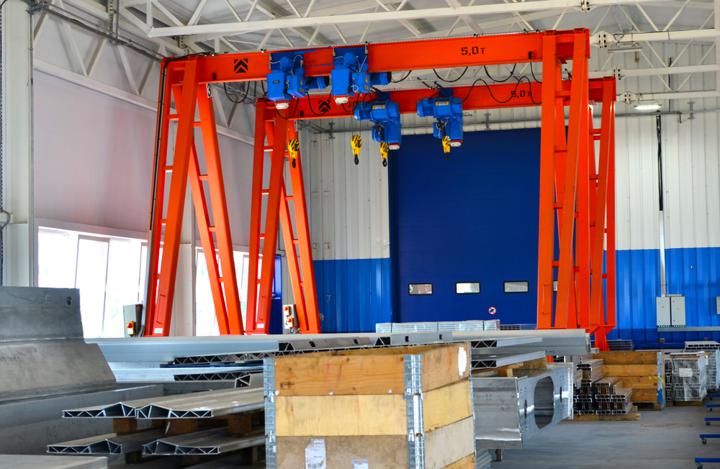
Now that we’ve looked at the advantages and drawbacks to top running bride cranes, let’s take a look at the second option, underhung bridge cranes.
As mentioned earlier, in this configuration, the crane trolley mounts to the bottom of the bridge girder instead of mounting on top and has wheels to move back and forth along the girder. The mounting location is typically inside the bottom of the I-beam flange. Since the entire assembly, including the trolley, motor, wire rope, and hook, is hanging below the bridge girder, the top hook height for these systems is significantly lower than that of a top running system. Having a lower top hook height means that if the headspace (or ceiling height) in the facility is low, you could be limited in the size of the object that you’re able to lift. This can present issues in some cases (e.g., if you’re needing to hoist one tall object over another).
The second potential drawback to an underhung bridge crane is the rated capacity that you can achieve. In a top running system, the crane trolley sits on top of the bridge girders, so the load is transferred down onto the bridge girders and runway beams. In the case of a double girder system, this can be designed for extreme loads. You’re more limited with an underhung configuration, however, because the load is bearing down on the wheels that are mounted inside of the bridge girder flange. Typically, the max capacity you can achieve with an underhung system is only around 10 tons. Since the lifting capacity is much lower on underhung cranes, the supporting beams (i.e., the runway beams and girder) can typically be much smaller than those used for top running cranes. You will still need to ensure that your roof structure is adequately designed to support the crane, but in most cases this supporting structure will be much less expensive than a top running system.
Another major advantage of underhung bridge cranes is the flexibility they permit to move throughout the space. As mentioned earlier, a top running bridge crane is limited in how close it can get to the walls because the hook is centered between two large girders. Even if you’re using a single girder system, you can run into similar issues due to spatial constraints dictated by the ceiling design. Underhung bridge cranes are able to get closer to the ends of the runways and bridge girders, providing more space in the facility which the underhung crane can access. The crane hook is also easier to handle by the operator as its smaller and has more flexibility from the bridge girder.
A few features of an underhung bridge crane include:
· Load Capacity: ¼-ton to 15 tons
· Typical Span: Less than 65 feet
· Typical Service: Light to medium duty
· Maximizes floor space
· Less expensive structure system compared to top running cranes
· More flexibility throughout facility space
· More difficult to service in comparison to top running cranes
So, what’s the best system for your needs?
We’ve discussed several key factors to consider as you’re evaluating whether to use an underhung or top running bridge crane at your facility. Some questions to ask yourself include:
· What is the heaviest object I’ll need to lift?
· What is the top hook height required to meet my lifting needs? To determine this, figure out the tallest object you’ll need to lift; how much height the rigging will add; the height of the tallest object you need to lift this object over; and provide a few feet of clearance between those two objects.
· Do I need to have flexibility to pick up objects close to the walls?
· How am I going to service and maintain the crane?
· What modifications do I need to make to the building’s support structure?
· Is this facility a new build? If so, you can incorporate the needs of the crane system into the structural design instead of needing to retrofit an existing system.
There are lots of things to consider when evaluating the best crane system to meet your needs. Fortunately, there are experts who specialize in designing and maintaining crane systems who can guide you through the entire process to ensure you end up with a system that keep you operating at full capacity. Crane Tech can take a look at your specific situation and help provide a crane recommendation which meets all your needs while optimizing cost. As crane experts, we are dedicated to providing unparalleled industry knowledge to inform your decision. To start the discussion, contact us today.